Insights
Mass Timber for Multifamily Housing: Sustainable, Fast, and Beautiful
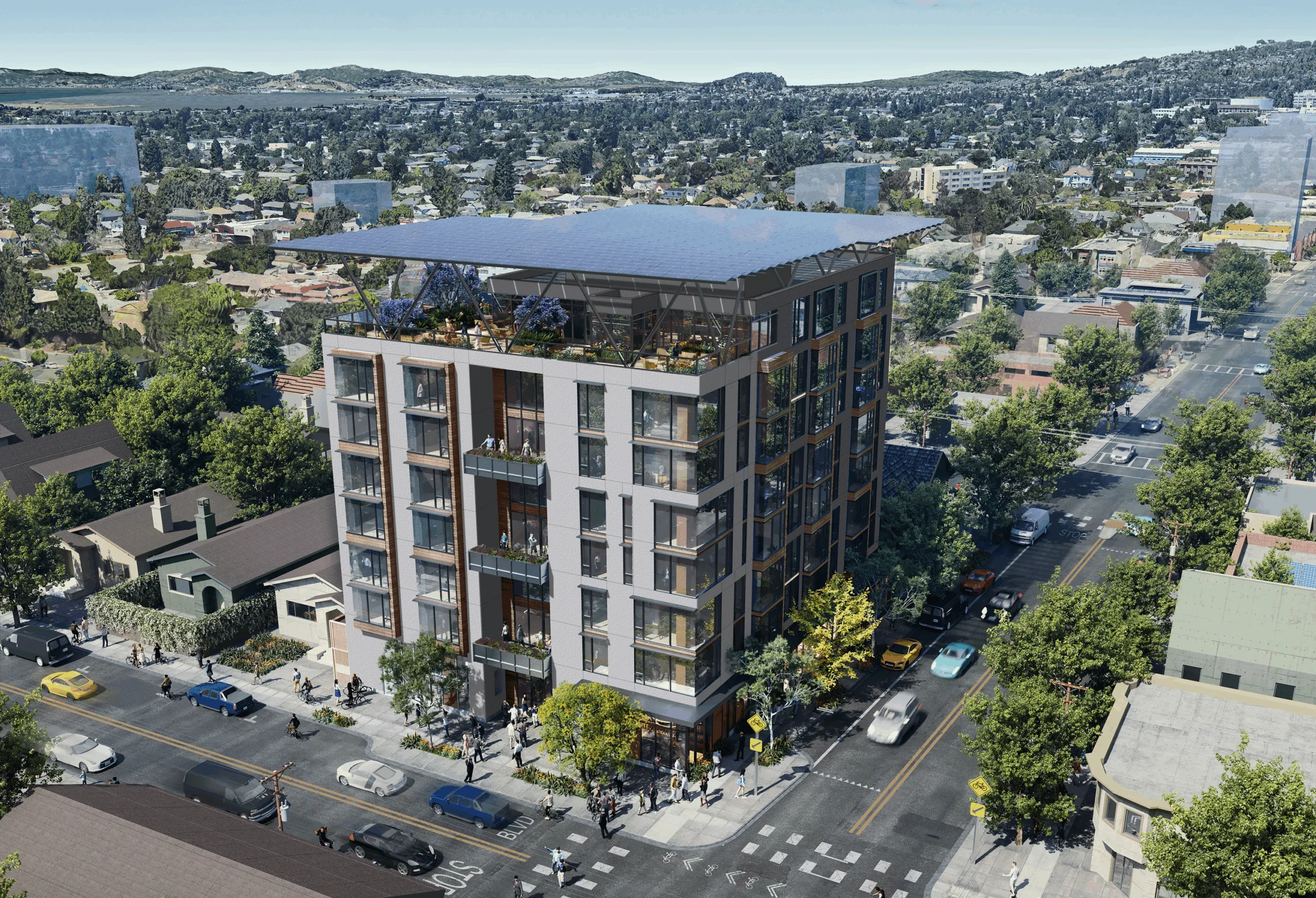
Mass timber for multifamily housing is no longer a far-fetched idea. Its use is rapidly gaining traction in the US thanks to its inherent benefits in environmental stewardship, speed to market, and natural beauty.
That said, not all mass timber buildings are created equally. Variations in cost, schedule, and carbon impact — not to mention fireproofing, acoustics, building enclosure, and roofing systems — all figure into a building’s performance and value over time.
In 2022, SCB and several of our industry partners set out to study the benefits of mass timber construction on multifamily developments through a study funded by a Wood Innovation Grant from the US Forest Service. The initiative challenged us to track, test, and iterate what we know about using mass timber by reimagining existing buildings in three distinct regions of the US: the Upper Midwest, Rocky Mountain Colorado, and the Southeast. Each design was held to the same floorplate, unit mix, and programmatic requirements as the original use to attain the most accurate results. We adhered to the Tall Mass Timber provisions of the 2021 and 2024 International Building Codes (depending on region).
“U.S. working forests in each of these regions can―and should―be part of the climate solution.”
Nicole St. Clair Knobloch
SCB collaborator and Principal at Olifant
Multifamily Housing Reimagined
After meeting with local chapters of the AIA to select optimal buildings for the case studies, the team conceptually redesigned buildings in Minneapolis, Denver, and Atlanta. Across all three, we revealed consistent benefits in speed and Global Warming Potential (GWP), and some varying results in cost.
Minneapolis
Stick-built
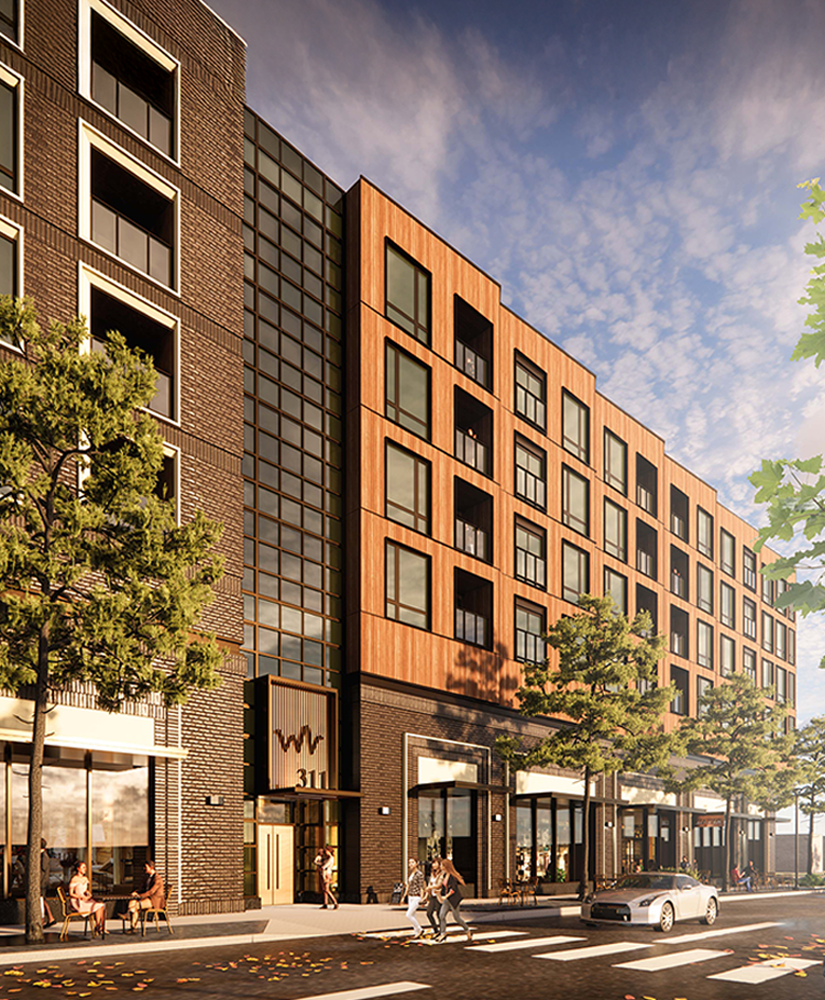
Denver
Cast-in-place concrete

Atlanta
Cast-in-place concrete
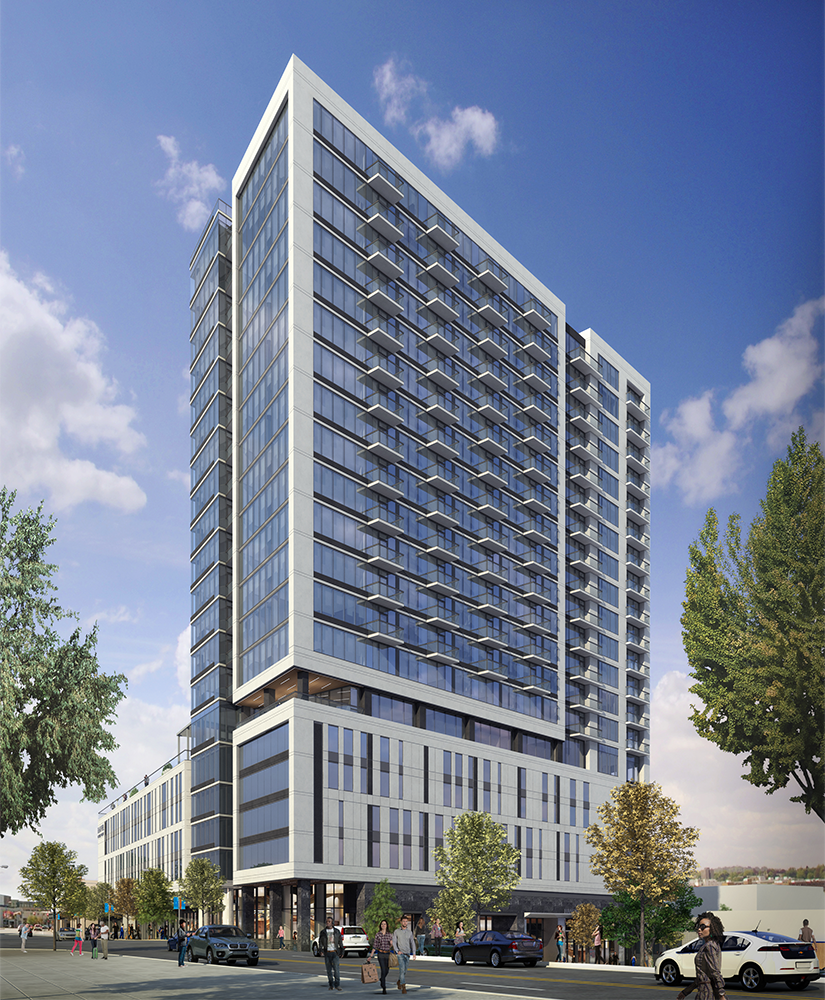
Here is a breakdown of our findings:
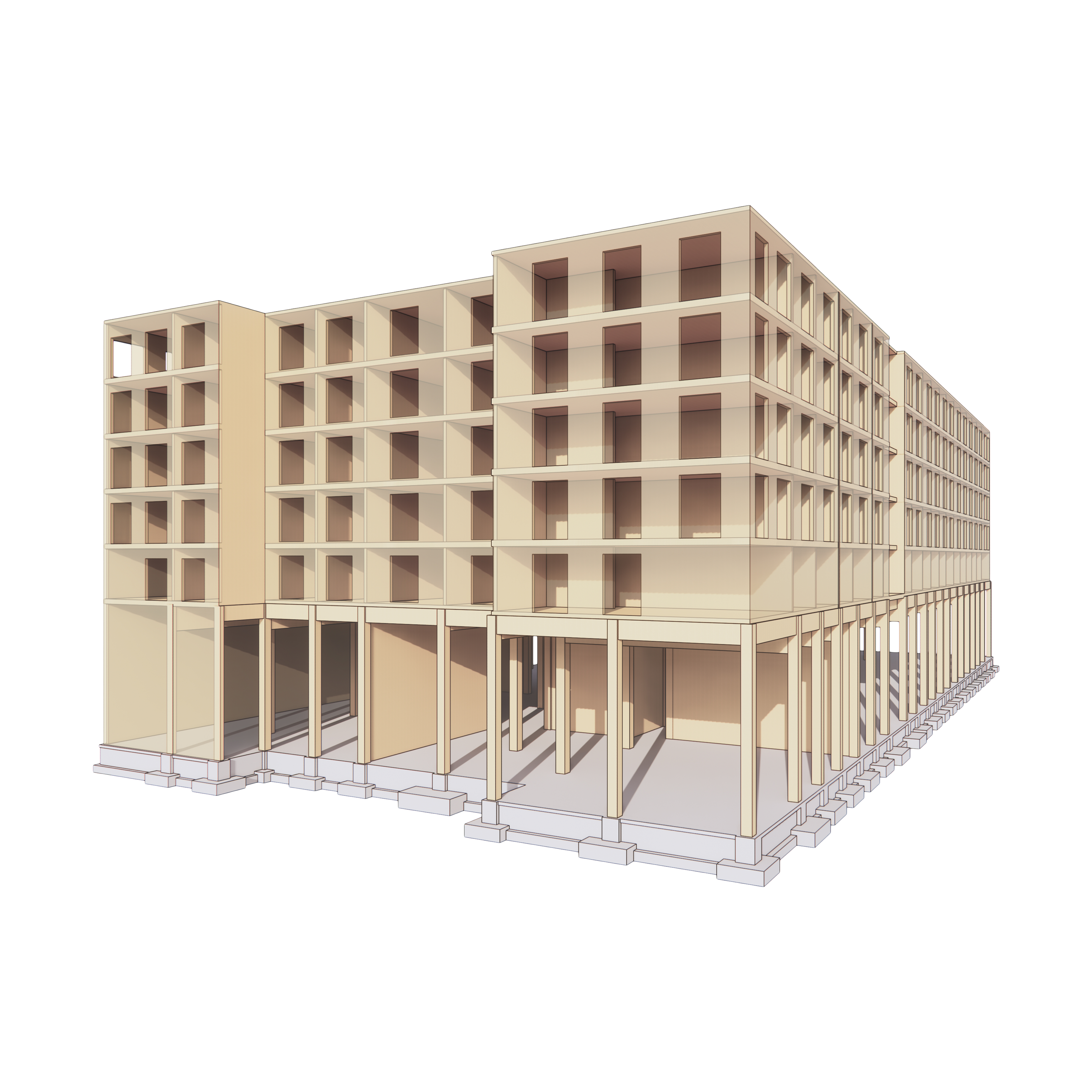
Big Sustainability in a Small Package
Case Study: Minneapolis, MN
IBC 2021 Type IV-C
Building Studied:
A seven-story stick-built residential building
- Climate: 42% lower GWP
- Cost: $16 more per square foot (3%)
- Schedule: Unchanged
Even though this project was originally designed as a traditional wood-frame structure, the new mass timber design simplified it further. Because the new mass timber provisions allow for a full seven stories, the project would require fewer trades, allow more streamlined coordination, and less fire separation requirements.
“The Sweet Spot”
Case Study: Denver, CO
IBC 2024 Type IV-B
Building Studied:
A 12-story cast-in-place concrete residential building
- Climate: 22% lower GWP
- Cost: $19 more per square foot (3%), largely due to fire protection requirements
- Schedule: 3.5 months faster than traditional construction
This building type and scale yielded the best of all worlds, with notable GWP reduction, very modest cost increase, and significant time savings in construction. The “sweet spot” that this building type falls into allows for a large structure with limited additional fire protection requirements and the ability to leave much of the mass timber exposed. The benefits are expanded even further with the most recent IBC code release.
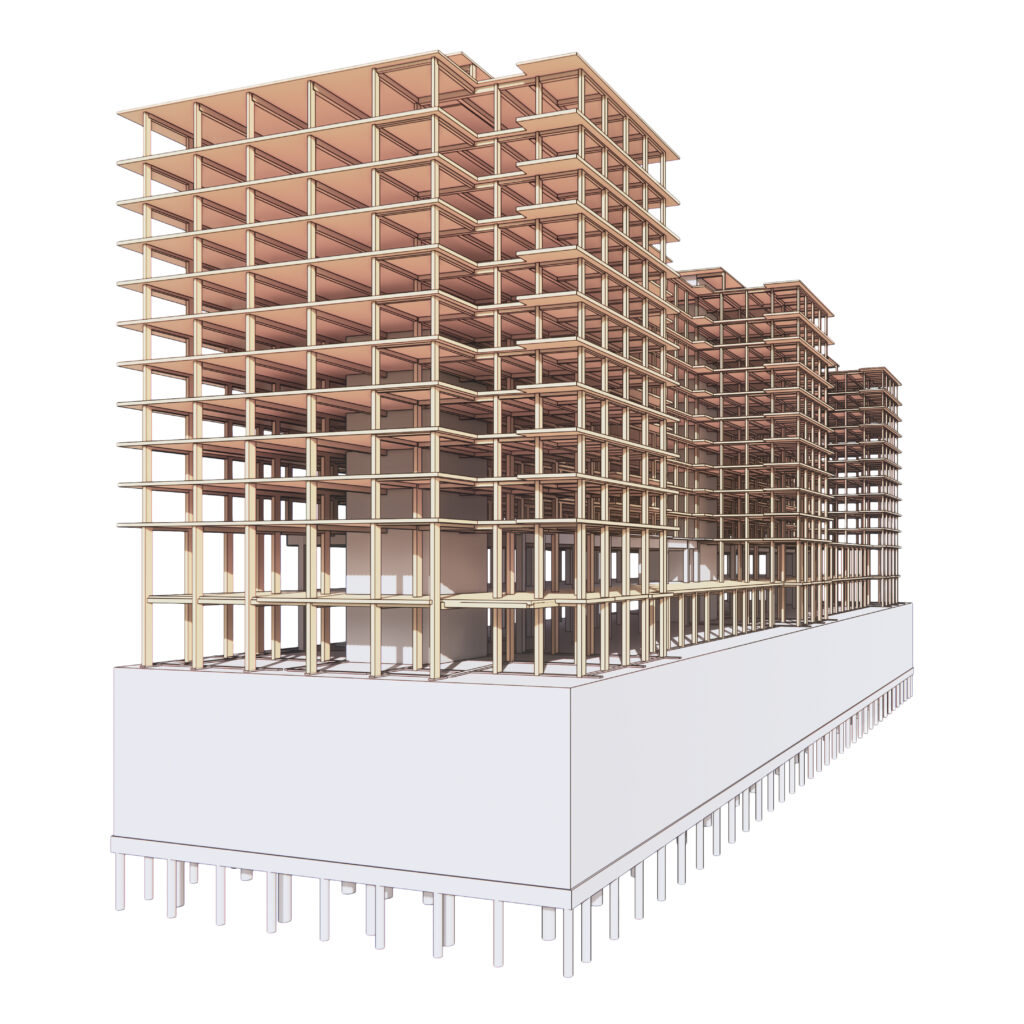
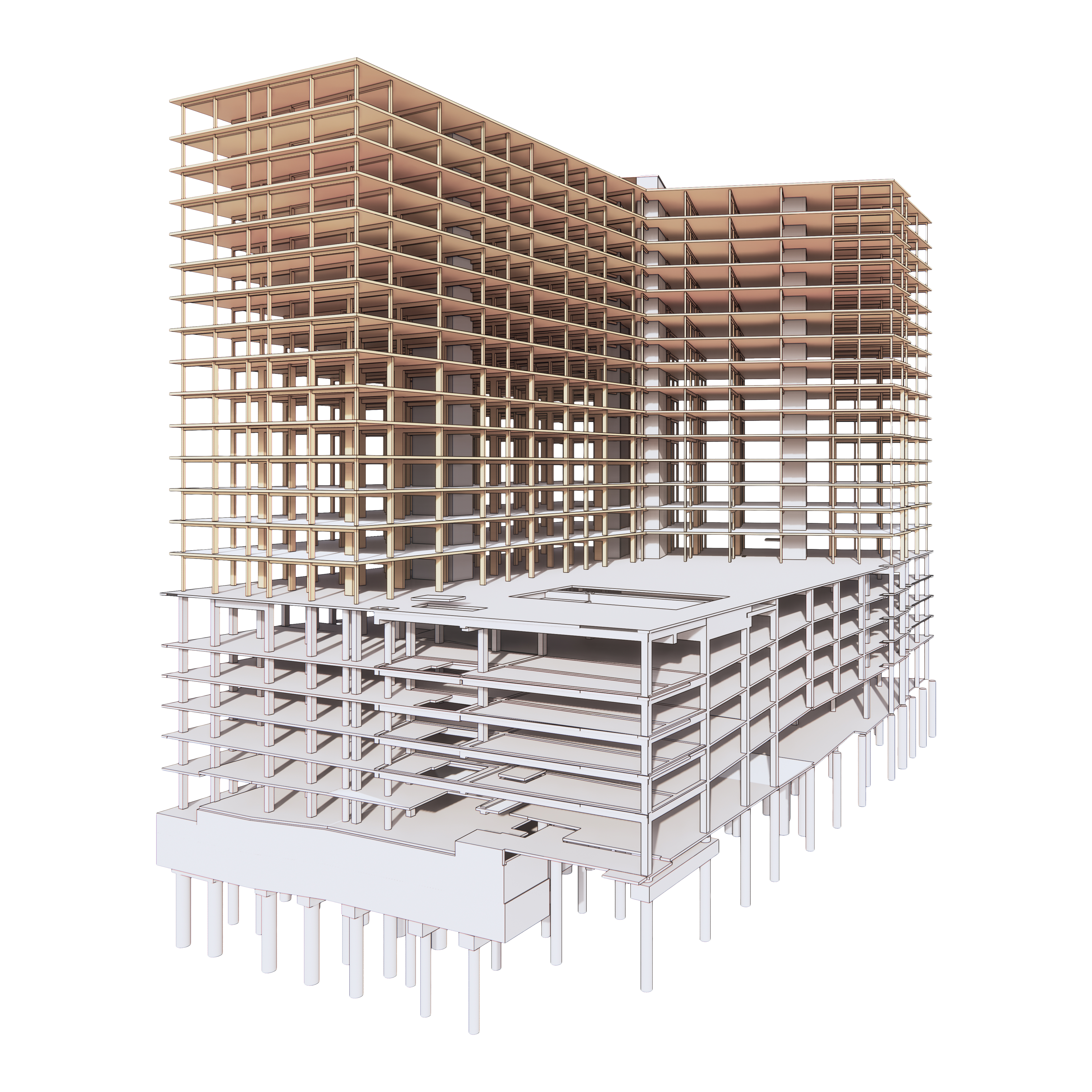
The Large-Scale Tradeoff
Case Study: Atlanta, GA
IBC 2021 Type IV-A
Building Studied:
A 21-story, cast-in-place concrete residential building
- Climate: 16% lower GWP
- Cost: $37 more per square foot (6%), primarily due to fire protection requirements
- Schedule: 3.5 months faster than traditional construction (unlike concrete, which requires time to cure; mass timber components are fully structured upon installation)
Despite the increase in cost, mass timber offered a major advantage in construction speed. And while this case study yielded the lowest GWP reduction among the three, its potential for meaningful carbon savings remains substantial given its larger scale.
A Cost Breakdown
During the study, we identified the major cost drivers and impacts between cast-in-place concrete superstructures and mass timber projects. We found that the costs would have been lower if the buildings had been originally designed using mass timber. Our cost analysis did not account for owner costs (and is based on residential areas only); garage costs were also excluded, since they remained a constant in each scenario.
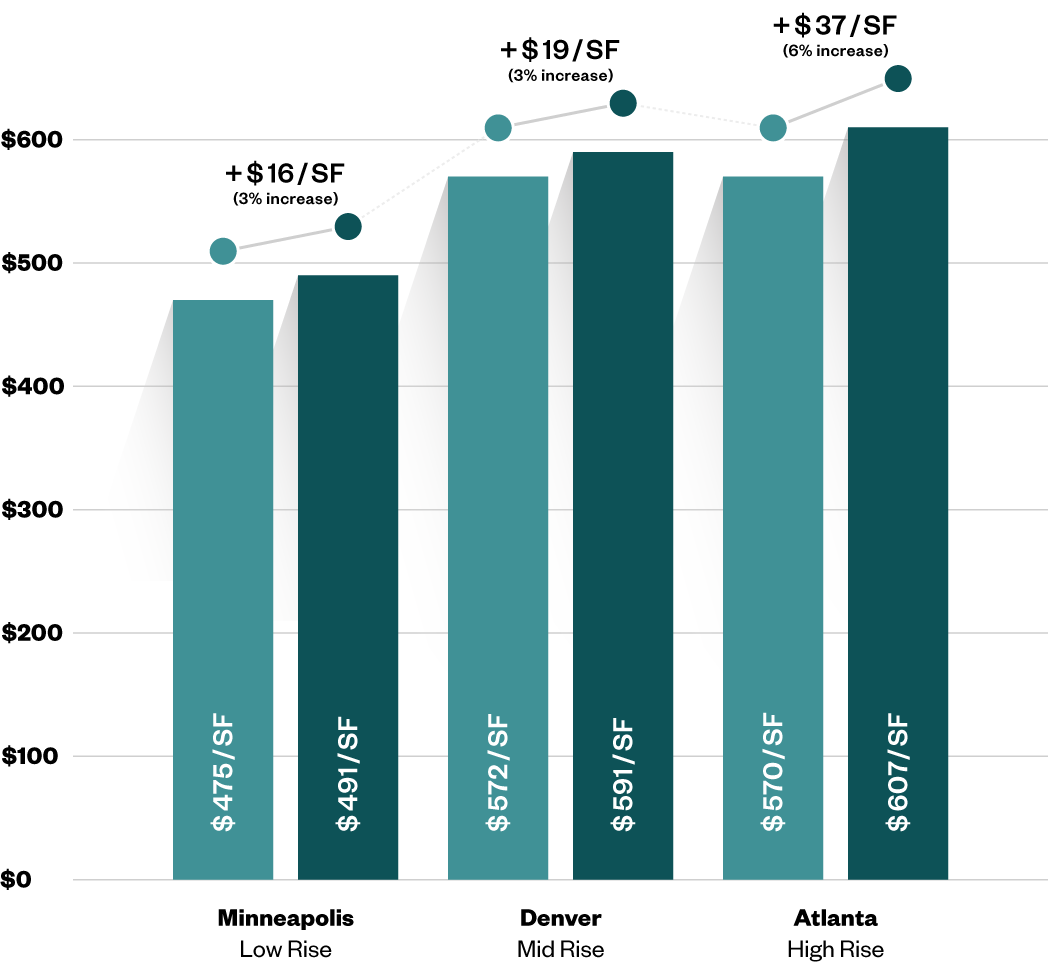
- Cast-in-place Concrete
- Mass Timber
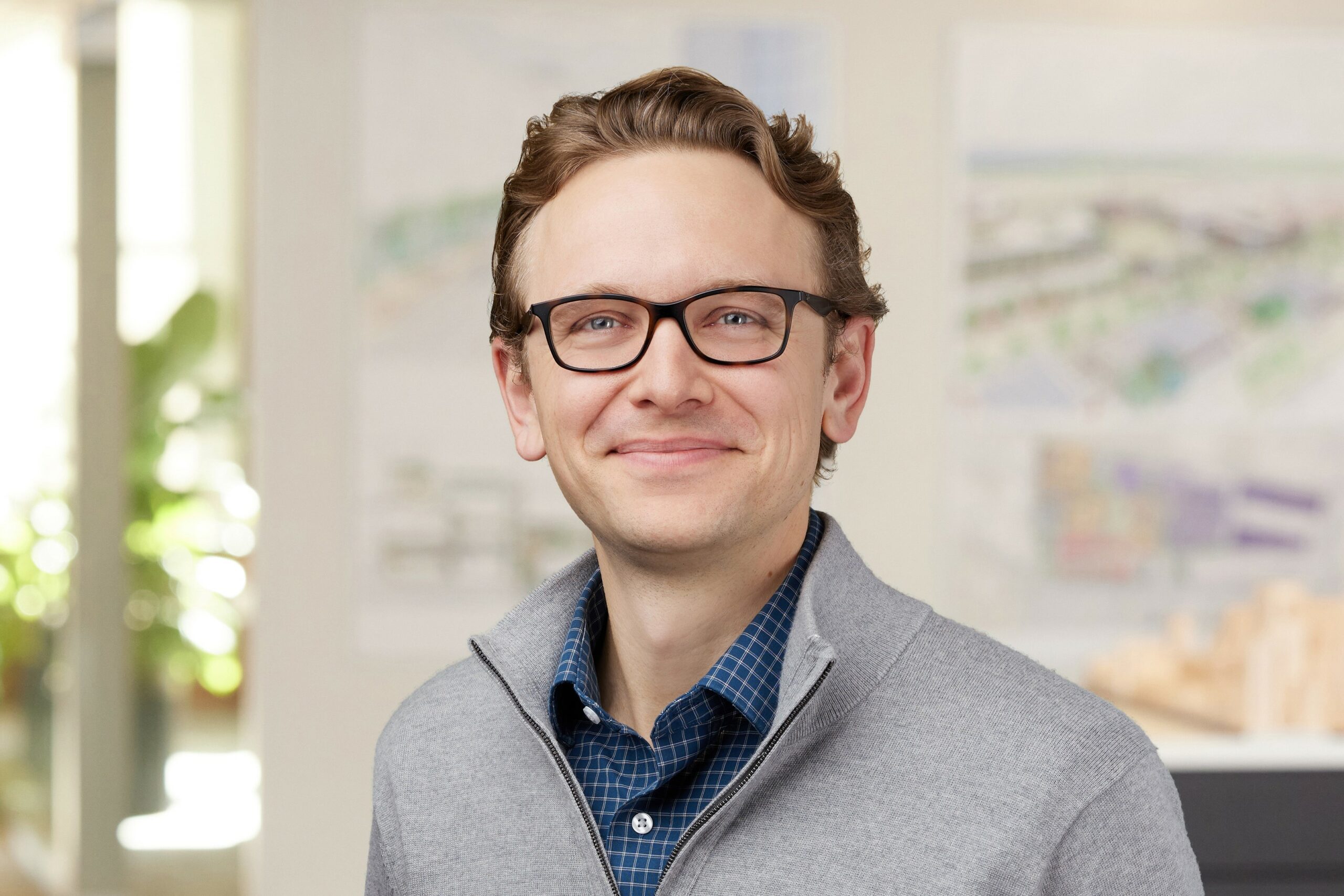
“If these buildings had been designed as mass timber from the outset, the inherent efficiencies would have likely reduced the cost increase at all building scales.”
Ben Harrison
Associate Principal
Read Bio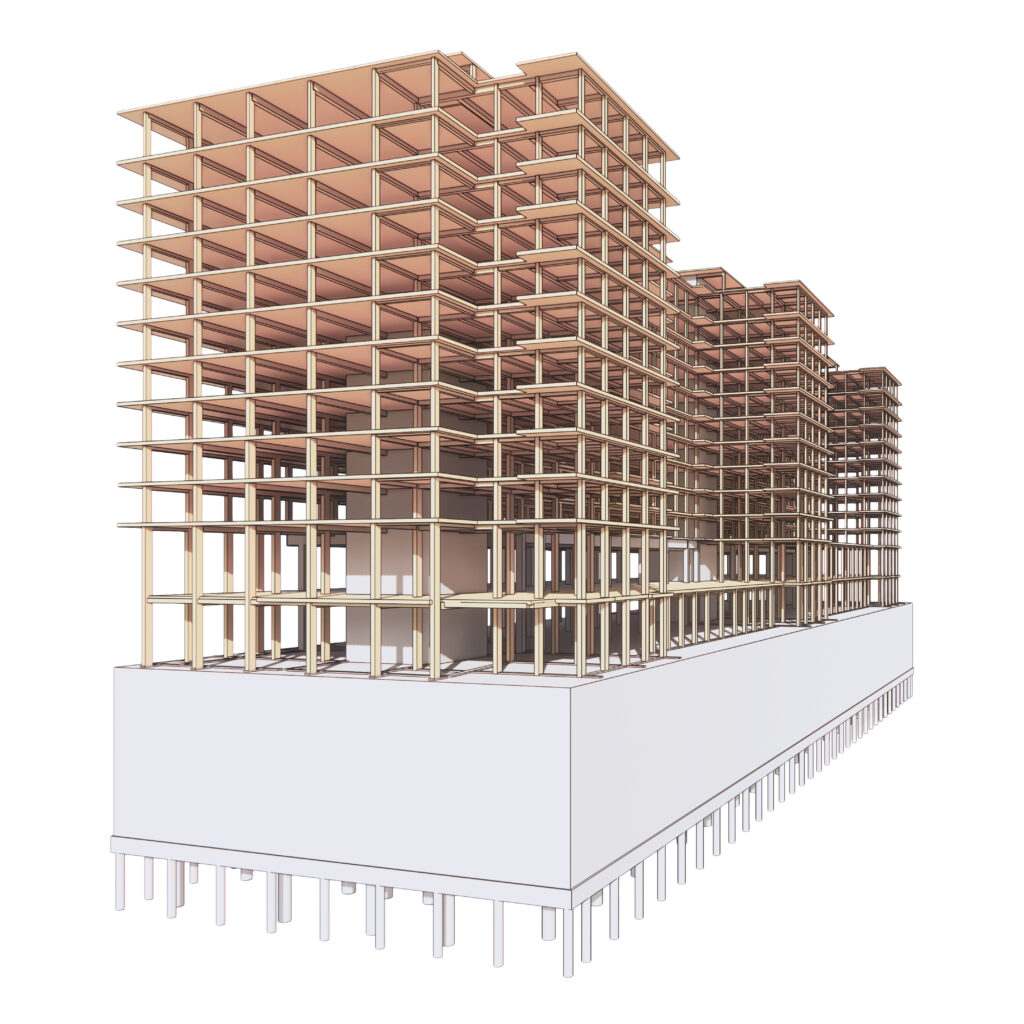
Which Building Type Comes Out Ahead?
Our team identified the proverbial “sweet spot” for mass timber construction: Type IV-B Construction reduced global warming potential by 22% (as compared with concrete) and increased cost by only 3%. Construction timelines were cut down by 3.5 months for tall and mid-rise mass timber, while balancing optimal density with both the schedule and environmental advantages. This method is gaining traction in cities like Boston and San Francisco, where mid-rise mass timber is seeing substantial gains for its sustainability and efficiency.
Mass Timber Code Adoption in the US:
We’re Getting There
Allowing more and larger mass-timber buildings is decided at the local/regional level, rather than on the national scale. This has its pros and cons. Right now, mass timber code changes are being adopted mostly in coastal, western, and southern US states; and less so across the Midwest and Southwest (with some exceptions, such as in Denver and Dallas).
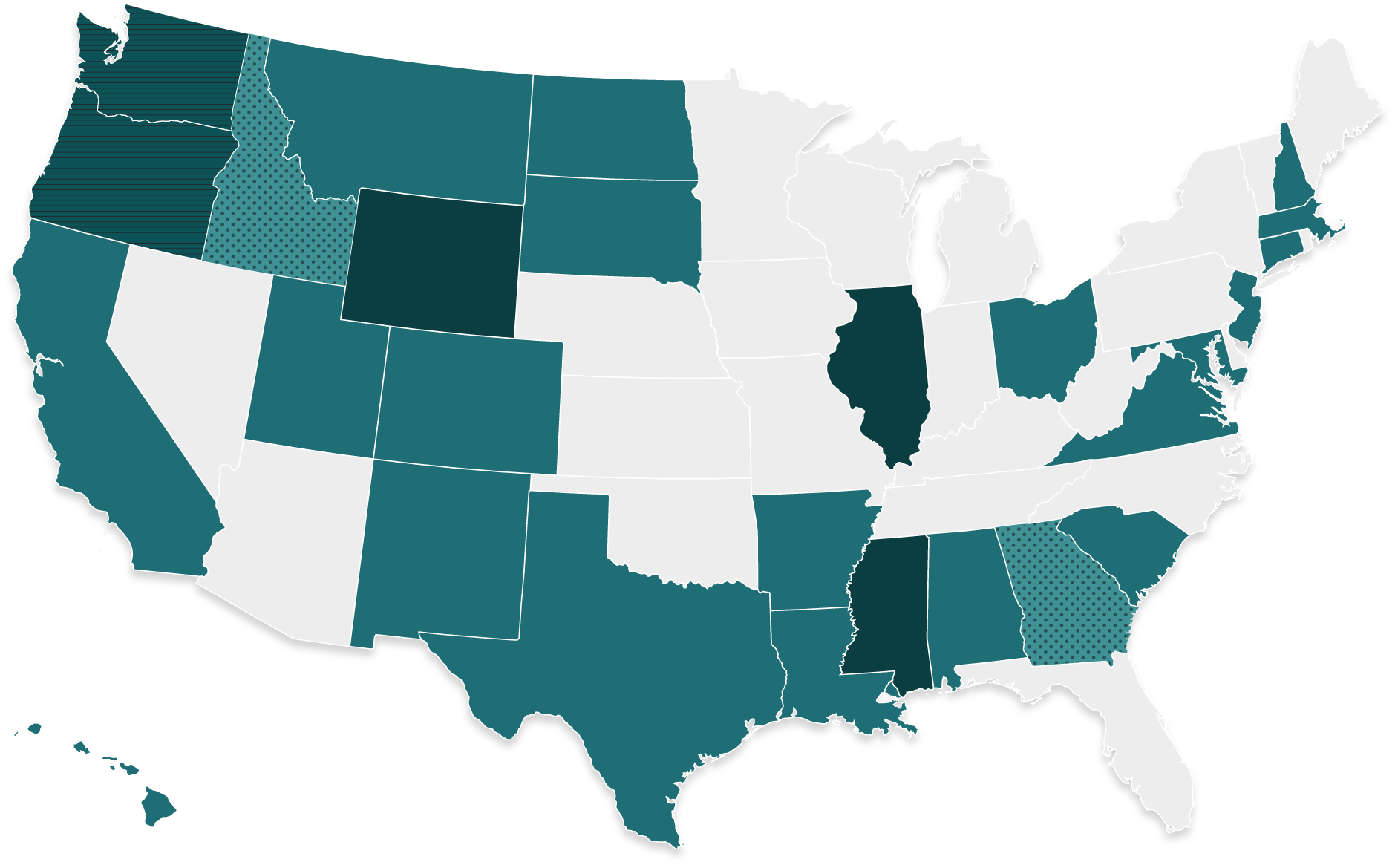
Tall Mass Timber Code Adoptions by State
- No Mass Timber Code Provisions
- 2021 IBC TMT Provisions
- 2021 IBC
- 2024 IBC TMT Provisions
- 2024 IBC
*As of Feb, 2024
Forestry Supply in the US
Interestingly, several of the areas adopting the newest changes in the code have the least access to sufficient forestry supply. By contrast, a city like Atlanta is well-positioned to welcome more mass timber construction due to its nearby forests and available wood.
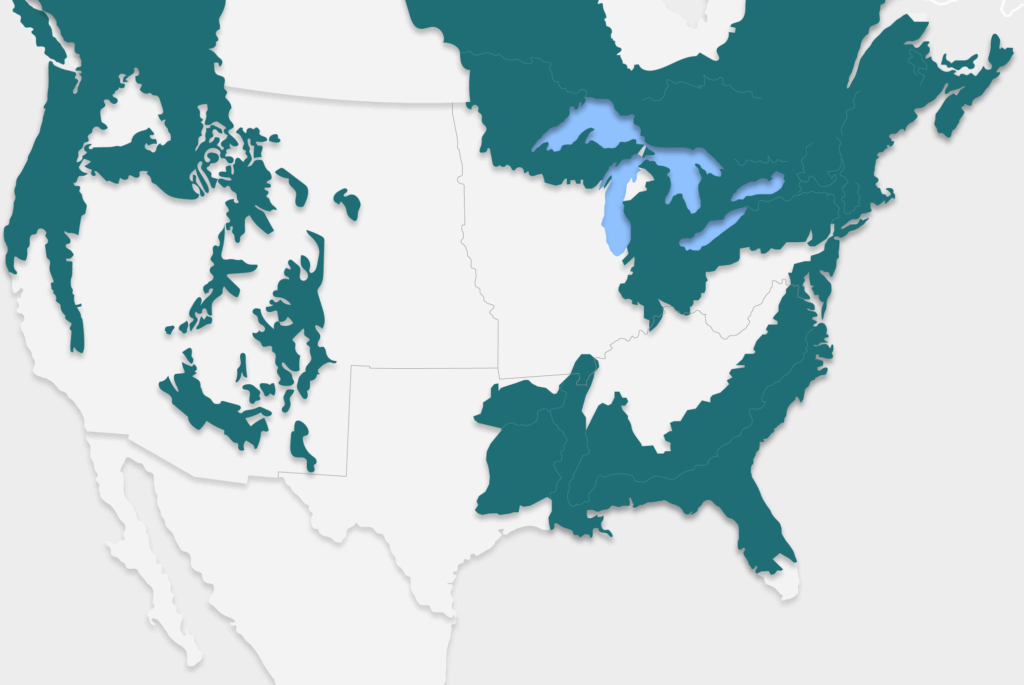
Facts Worth Knowing
While the actual engineering methods for fabricating mass timber have been around for decades, local codes are finally catching up to the potential of its advantages. In addition, achieving code variances was traditionally far more of a headache than it is today. Securing as-of-right building approval has always been the preferred route (faster and more cost-friendly), but these codes created tighter constraints on design possibilities for mass timber buildings. Now, as more cities and regions embrace new and future codes, tall mass timber construction is easier to shepherd through the approvals process for all involved.
IBC 2024 Updates
There are new provisions for Type IV-B that reduce protective timber requirements. This is a good thing. Wider adoption of this code will allow more projects of this type.
Acoustic Treatment
Acoustic floor treatments required by code contribute a lot to carbon impact. With better and more sustainable underlayment products, environmental reductions will keep improving.
Parking Structures
Concrete parking podiums account for over half of a building’s global warming potential. Reducing parking significantly lowers the overall carbon footprint.
More on the Three Regions Explore Mass Timber Study: SCB worked in close partnership with structural engineering firm LeMessurier and national construction firm Turner Construction, with the support of Springboard Forestry and local AIA chapters in Boston and in each case study location. The grant was secured by pioneering work by Olifant LLC and Lambert Sustainability, both of Boston.